‘Launch Vegas’ Marble Launcher
Perpetual Marble Launcher
February - March 2023
How can I design a mechanical, desktop, perpetual marble launching machine?
For ME102: Foundations of Product Realization, we were tasked with creating a ‘perpetual marble launcher’ using mechanical stock components, constructed of only hardware, acrylic, 3D printed materials. It had to have all mechanisms visible and serviceable, cost less than $40, containing both a “launcher” and a “hopper” component.
February - March 2023
How can I design a mechanical, desktop, perpetual marble launching machine?
For ME102: Foundations of Product Realization, we were tasked with creating a ‘perpetual marble launcher’ using mechanical stock components, constructed of only hardware, acrylic, 3D printed materials. It had to have all mechanisms visible and serviceable, cost less than $40, containing both a “launcher” and a “hopper” component.
Skills:
- Fusion 360 CAD
- Laser Cutting
- Iterative Prototyping
- 3D Printing
- Hardware
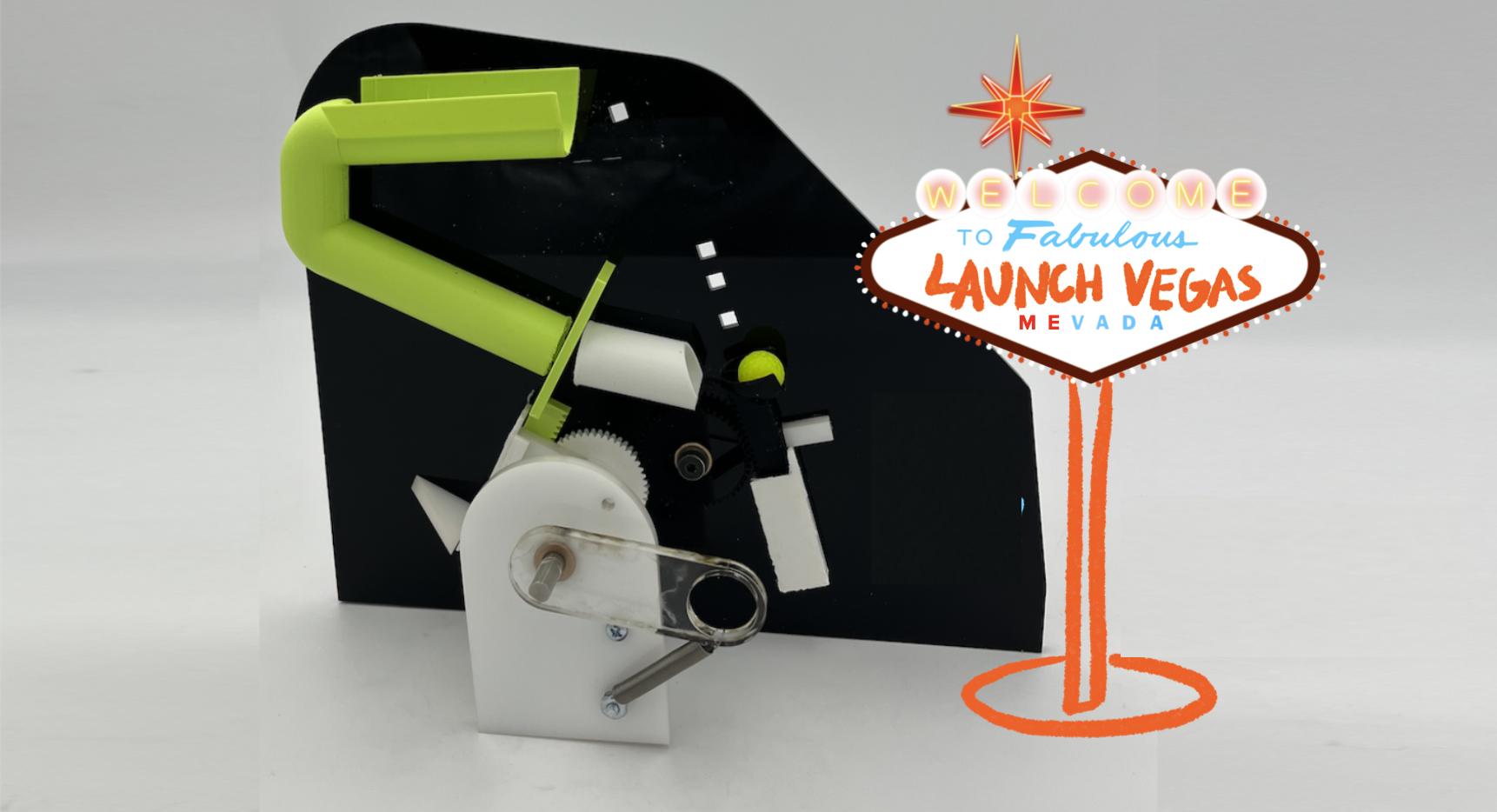
Launcher Requirements:
- Launch only one marble at a time
- Input must be operated with one hand, use rotary motion (less than 360 degrees), and reset on its own using a spring
Hopper Requirements:
- Store at least 5 marbles in hopper, loaded once without positional preference
- Marble must be fed back into hopper upon actuation
- Marbles must experience vertical height difference of 3 inches throughout journey
Concept Sketches

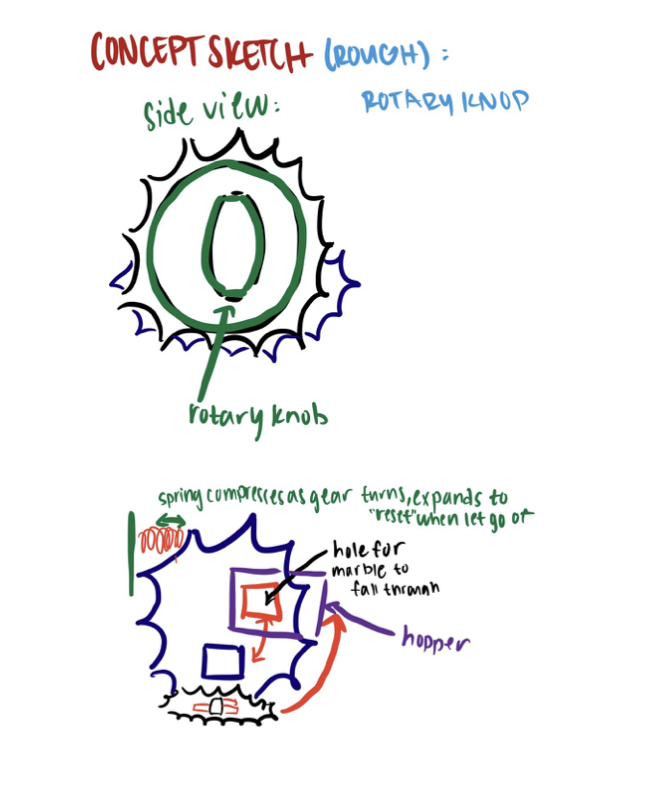


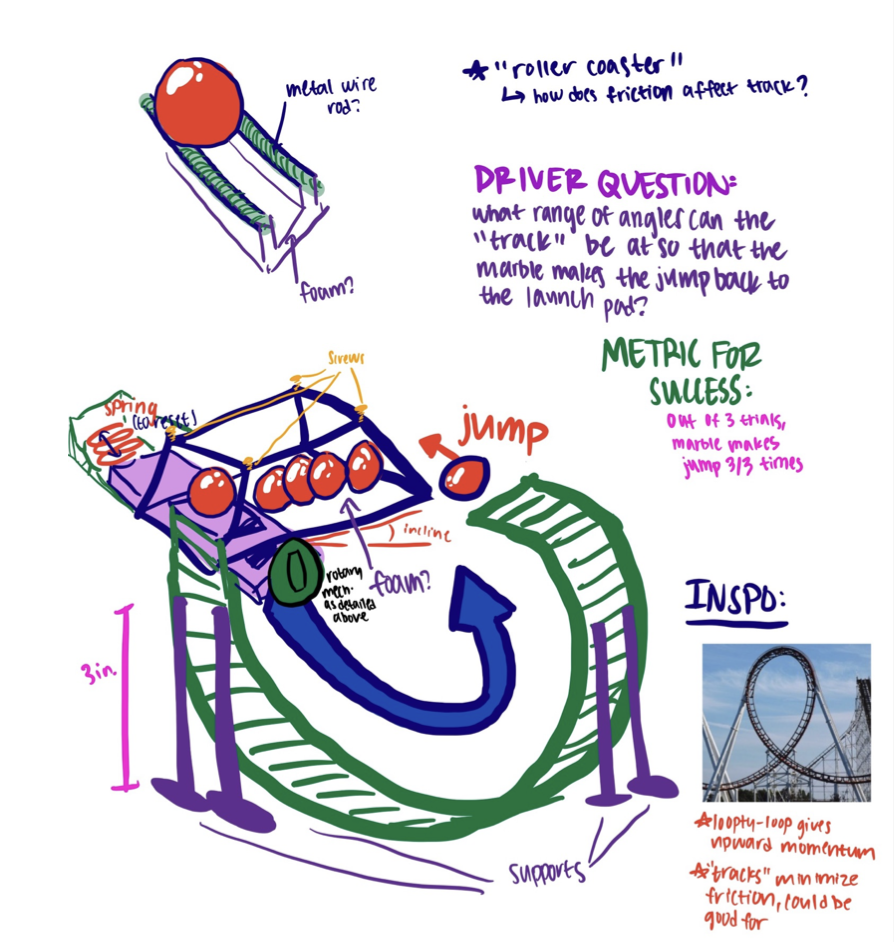
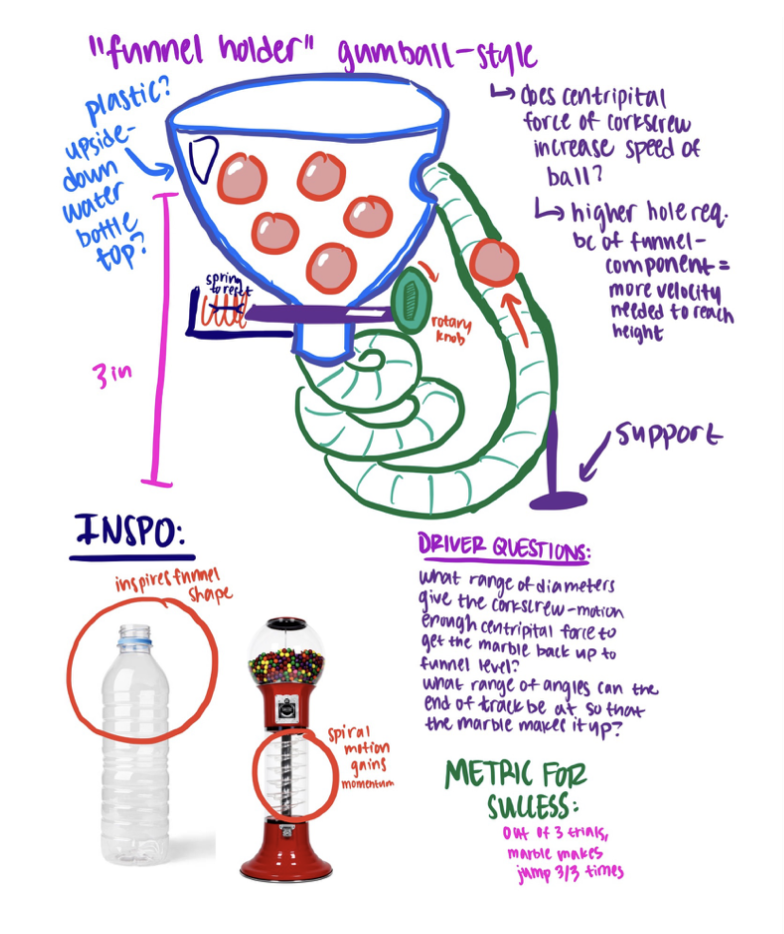
Benchmarking:
‘The Launcher’
‘The Launcher’
1
“Vertical Launcher”:
- Gives the marble both initial velocity, as well as utilizing gravity, making it the most likely to actually give the marble enough momentum to make the jump
- The shape of the track uses minimal friction, which might risk slowing the marble down

2
“Roller Coaster”:
- Relies solely on the force of gravity to propel the marble
- I worry that the force lost to friction will leave the marble unable to return to the hopper
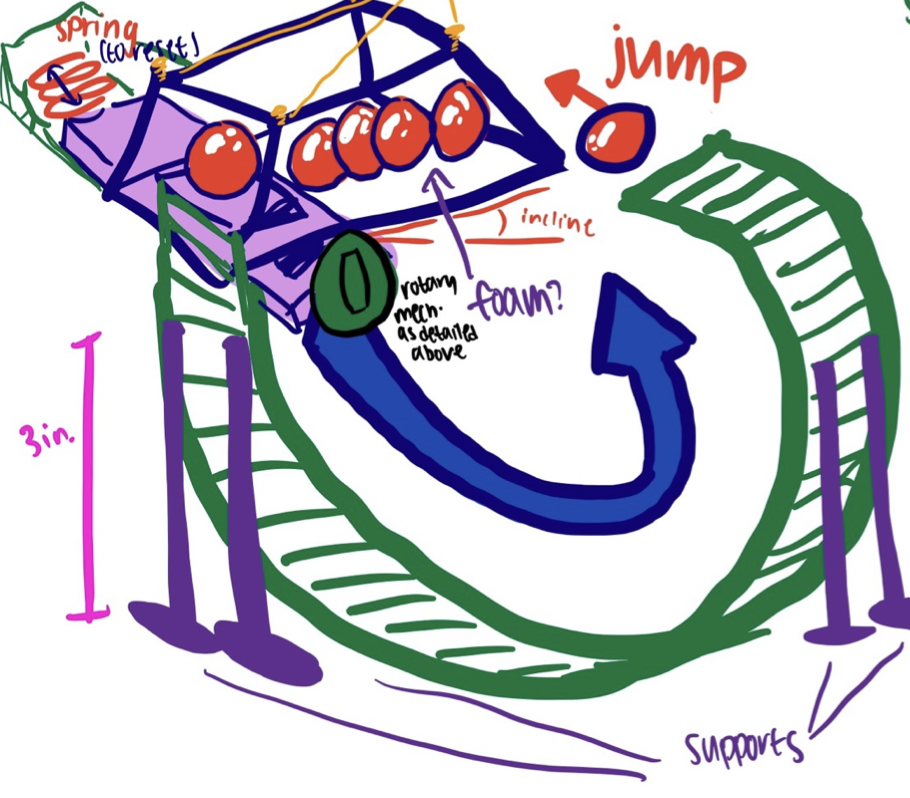
3
“Gumball-Style”:
- Worried that the centripetal force won’t garner enough speed to make the jump, and that the friction of the longer track will slow the marble down so much that it can’t make its way back up
- With no initial velocity, it seems like the slowest of the three options

Benchmarking:
‘The Hopper’
Original Hopper:
- Traditional funnel can load 5 marbles at a time without preference to order
- Risks marbles getting stopped up in the chute
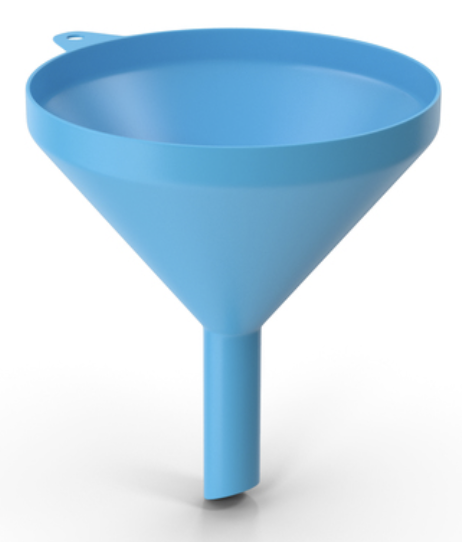
Modified Hopper:
- Have funnel lead to horizontal tube shape, so that balls fall in and assemble into line
- Lined marbles prevent clogging
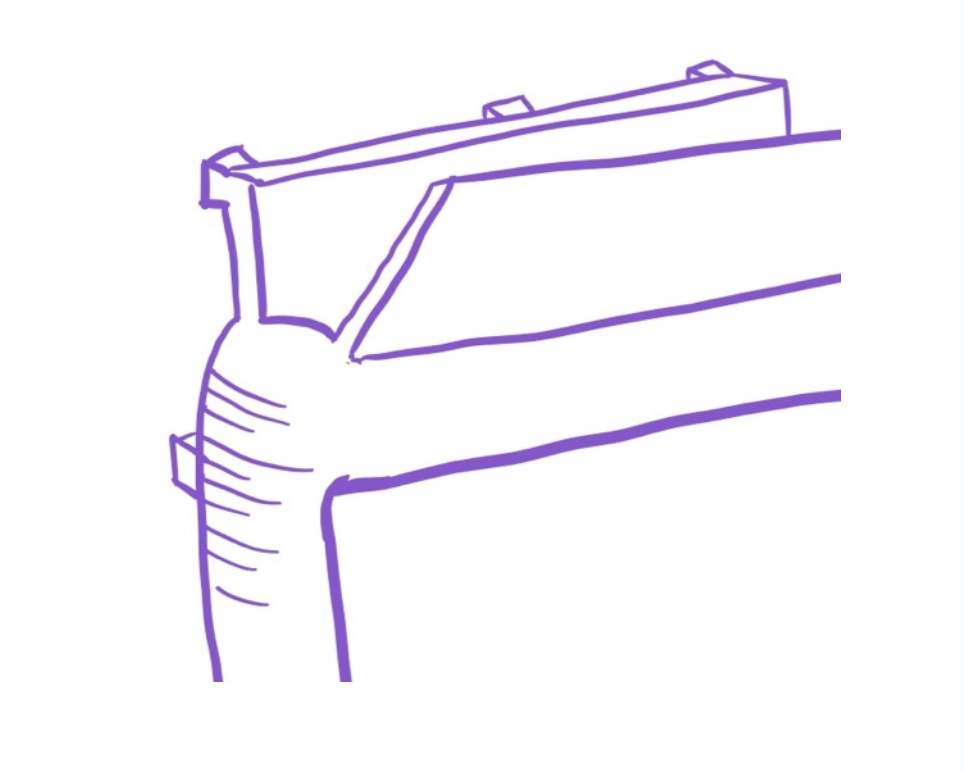
Iterative Prototyping
Rapid Prototype:
Materials:
- Cardboard
- Foam core
- Hot glue
- Coffee stir
Purpose:
- Better understand how gears interact
- Model candy-machine style hopper ball-dropping interaction


Metrics for Success:
Takeaways:
- When turned 3 times, the gear returns to its initial resting state 3/3 times
Takeaways:
- Material Importance: the material interaction was inconsistent due to foam-core being weaker. Pushed me to use laser-cut material in next prototype.
- Successful in modeling the subsystem
Hi-Fi Prototype:
Materials:
- Laser-cut acrylic
- Compression spring
- Hot glue
- Screw
Purpose:
- Test the range of heights for which a marble can be launched and returned to the original funnel position
- Model launcher on more durable materials, implementing compression spring
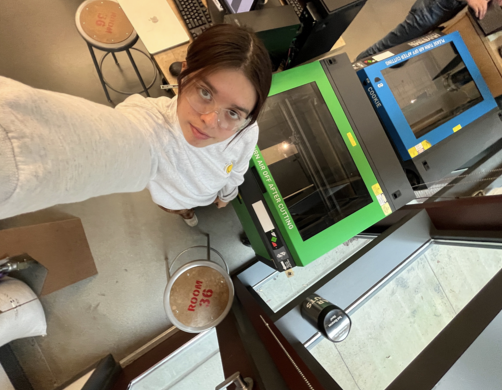


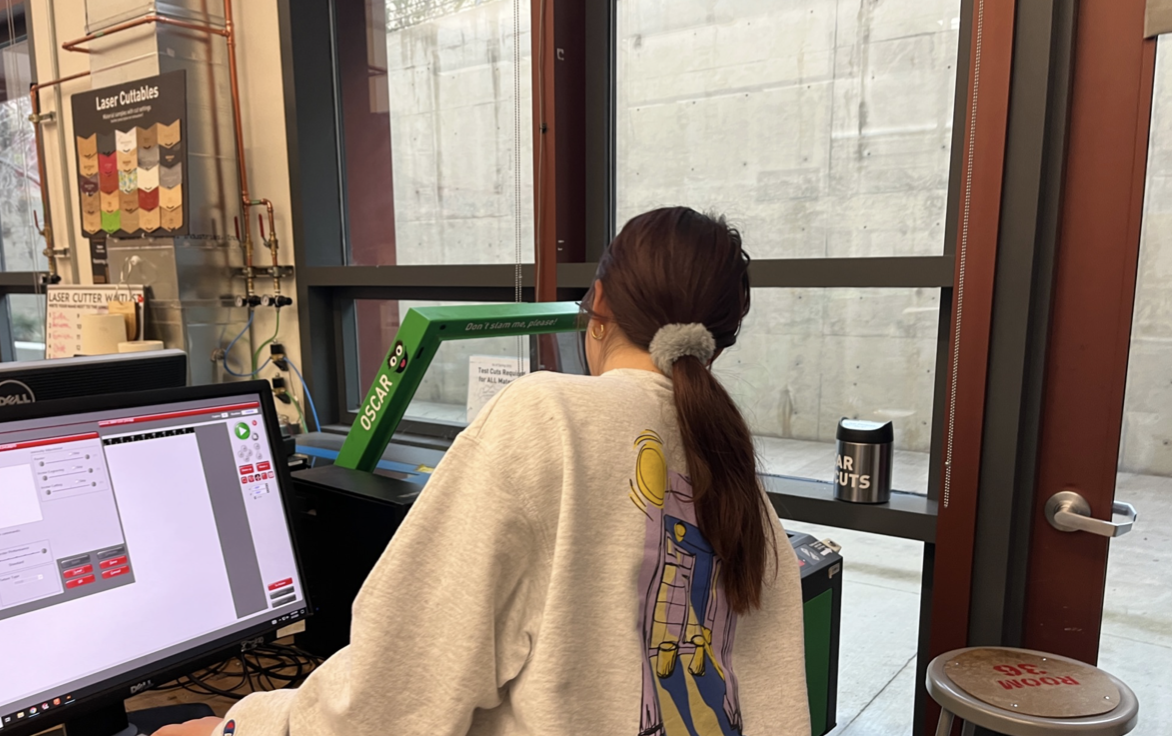
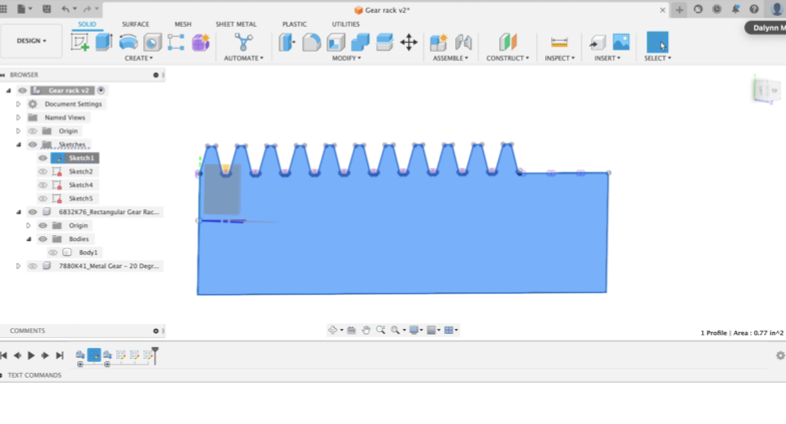

Takeaways:
- Pivot to vertical launch: with the provided compression spring, there was no angle except for fully vertical in which a marble could be launched the three inches
- Increase gear size: Small gears make it more difficult to turn the launcher
Functional Prototype:
Goal:
- Break down and test each specific subsystem

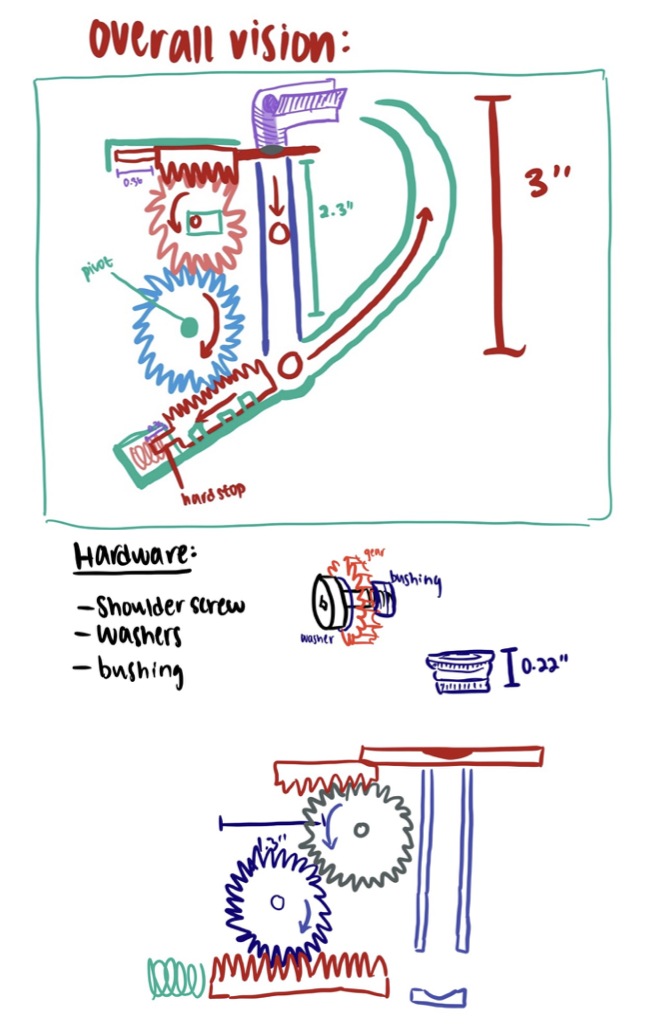
Defining Subsystems
Subsystem #1:

Identifying exact McCarr Gear:
![]()

Subsystem #2:
![]()
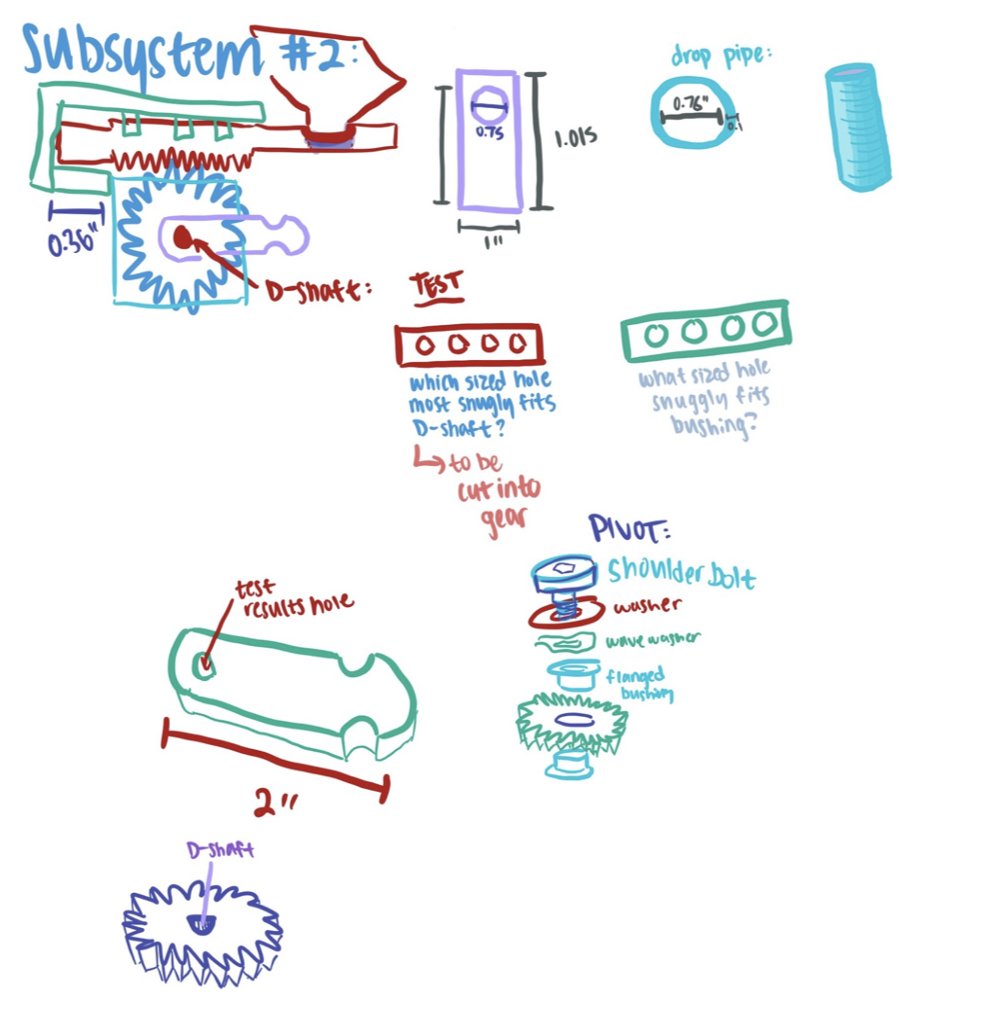
Driver Question:
![]()
- What diameters of bushing and D-shaft holes fits the D-shaft and bushing snugly?
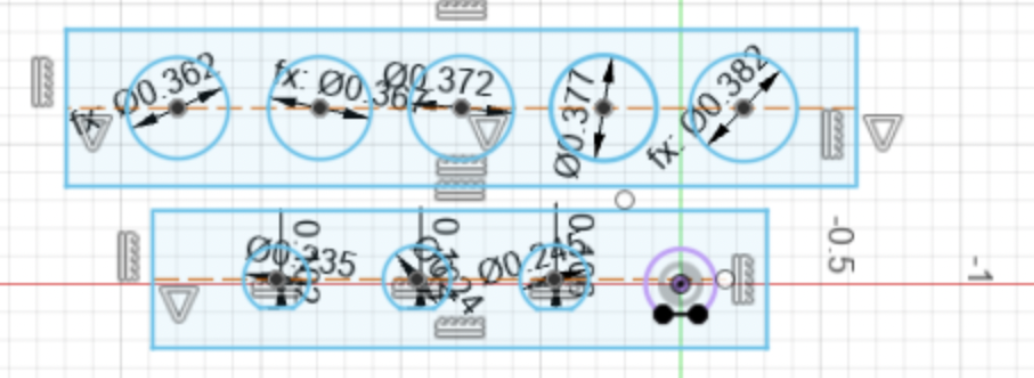


Subsystem #3:
![]()
![]()
![]()
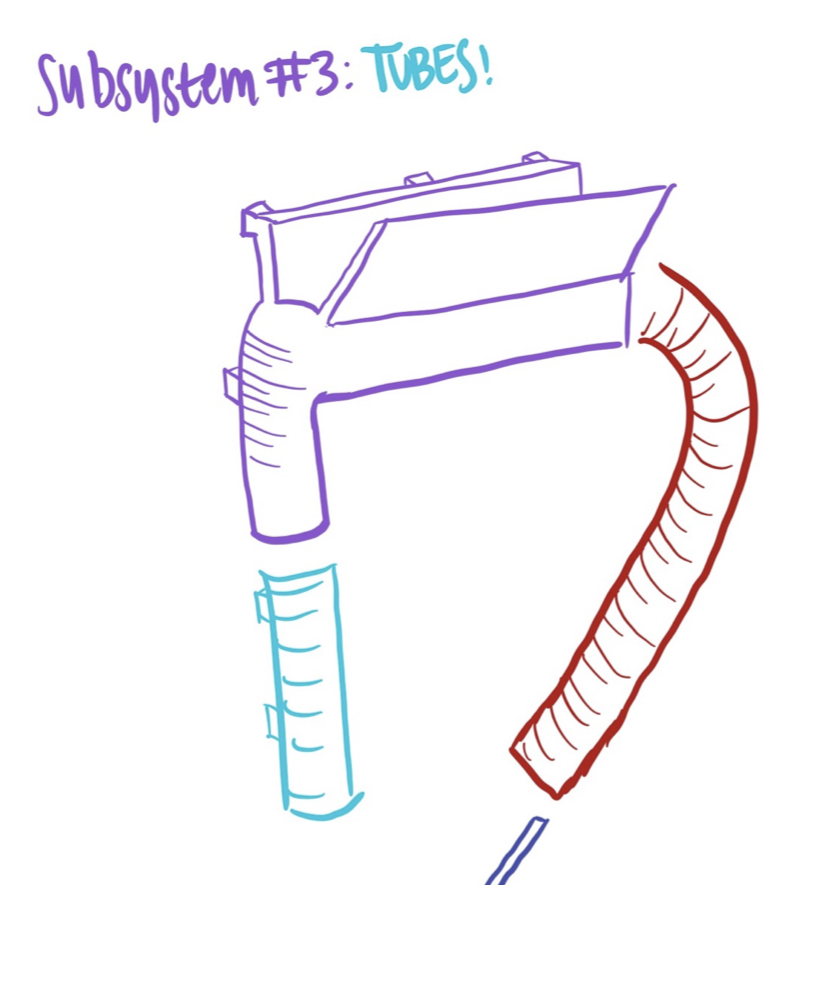

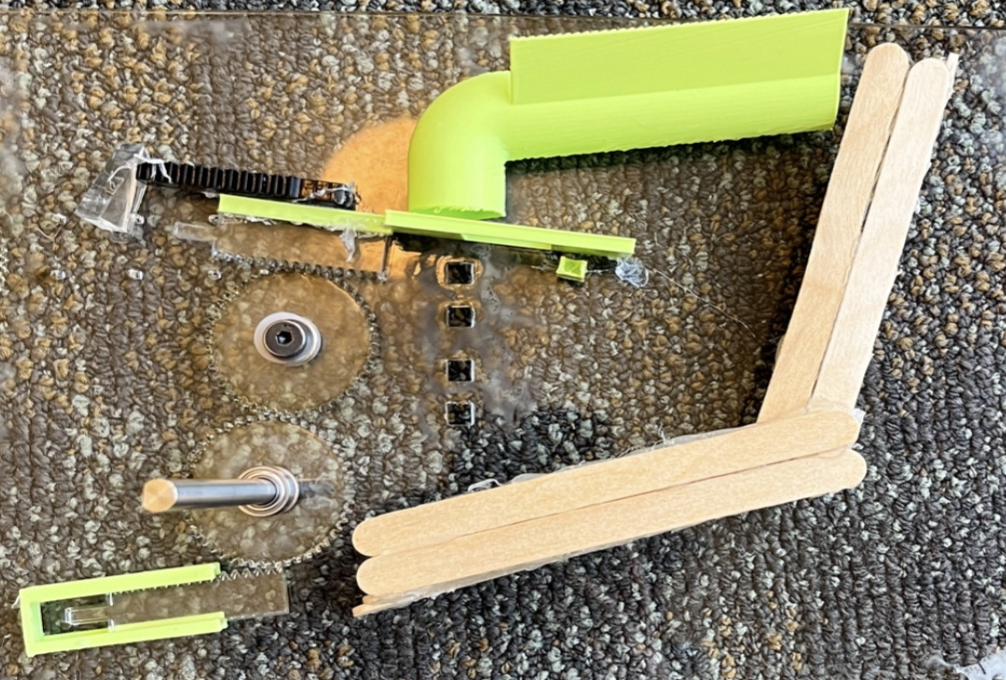
Driver Question:
![]()
![]()
![]()
- What shaped hopper can hold 5 marbles, inputted without regard to order, without jamming the tube?

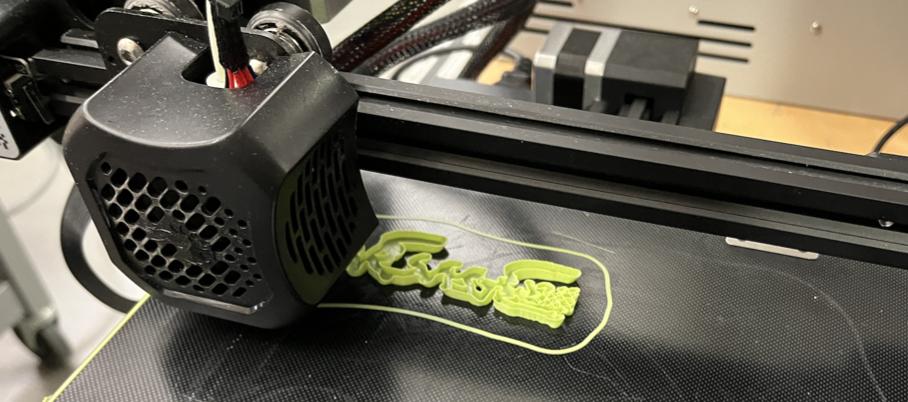
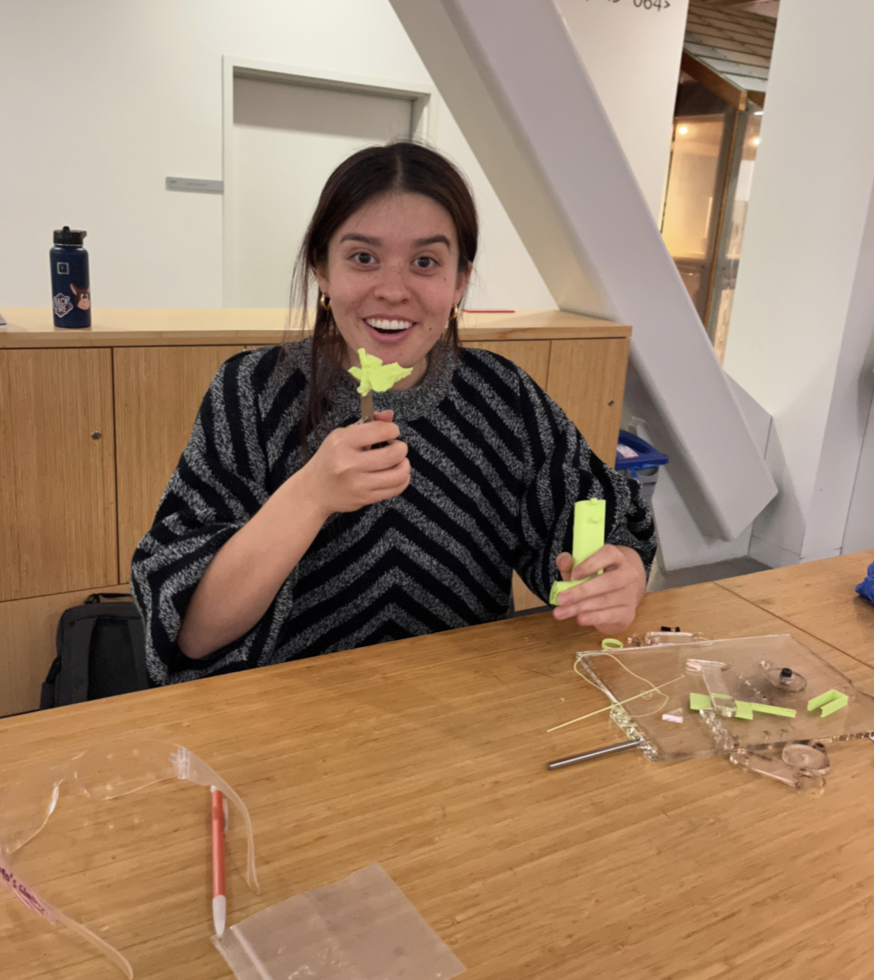
Final Construction

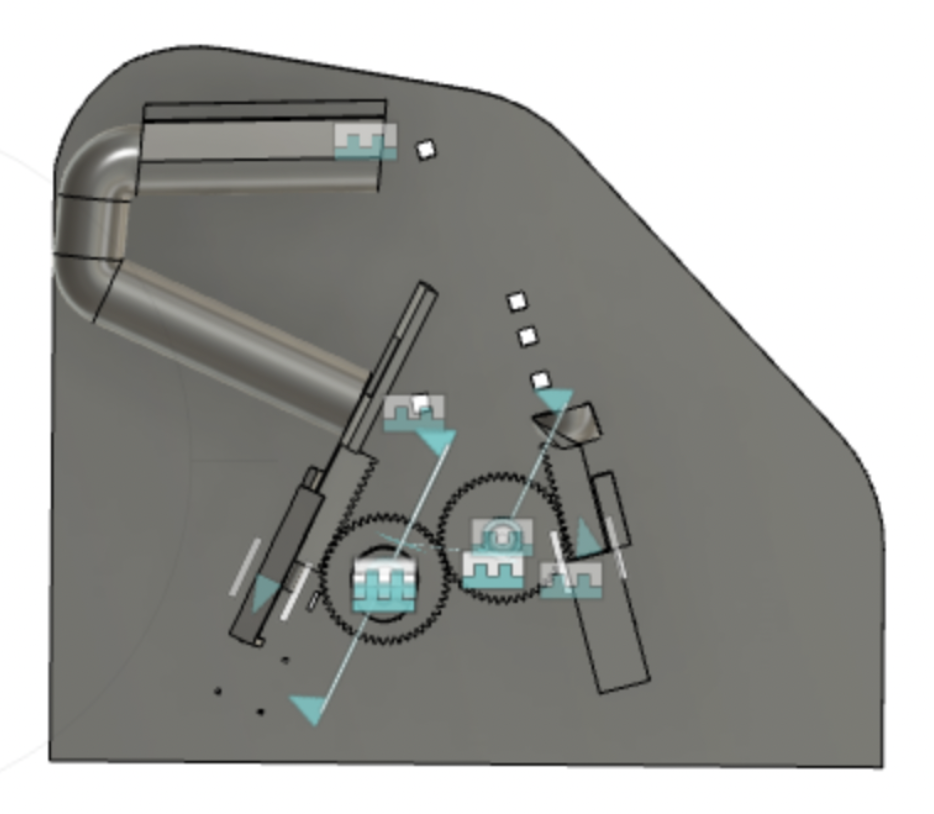
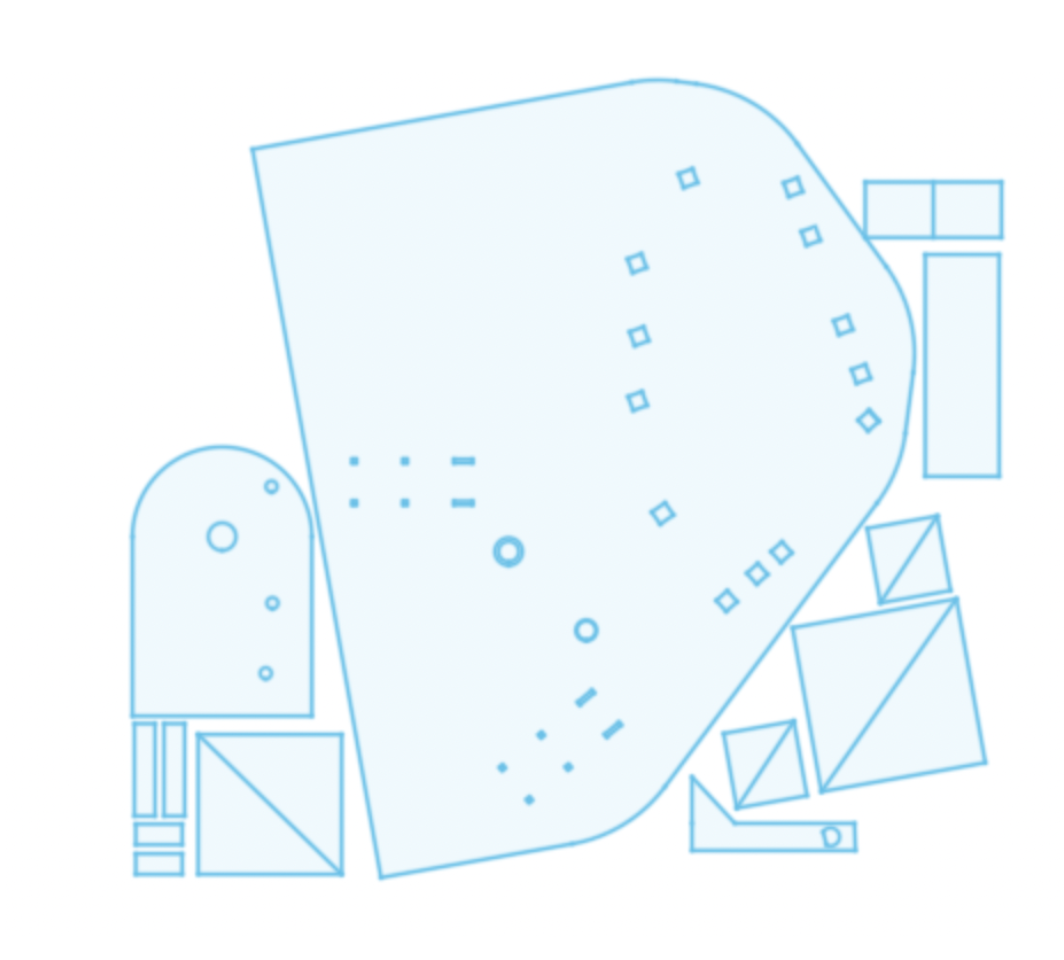
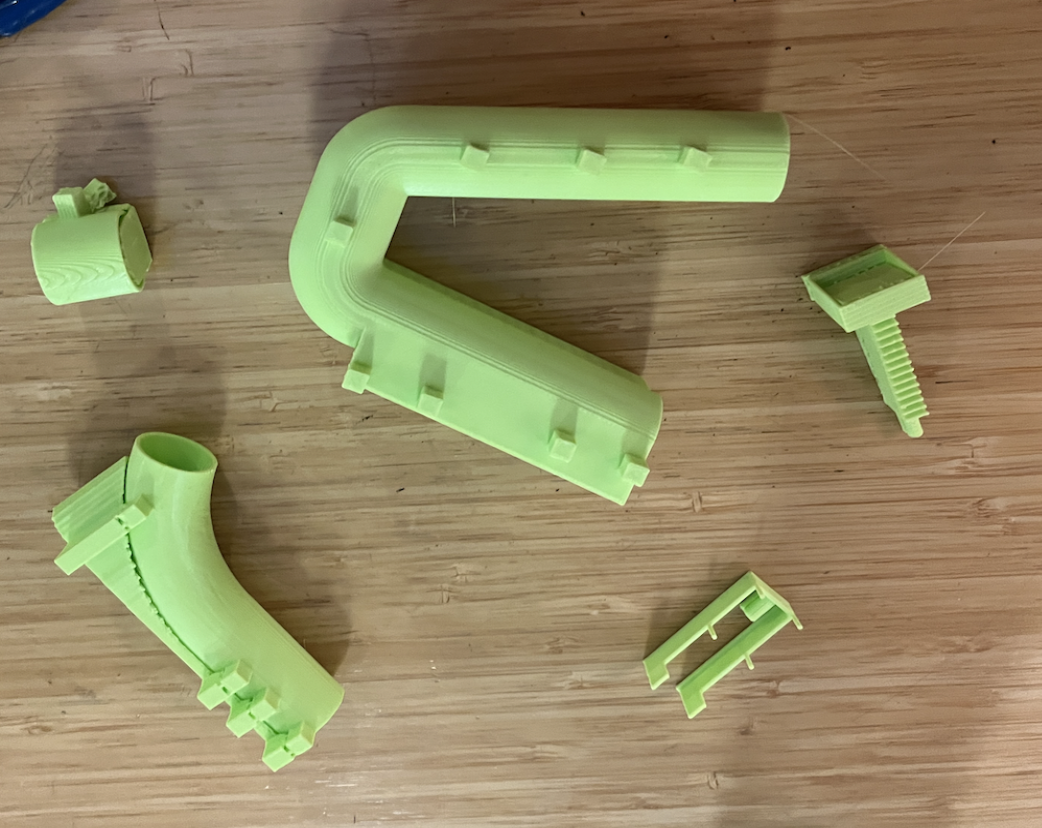

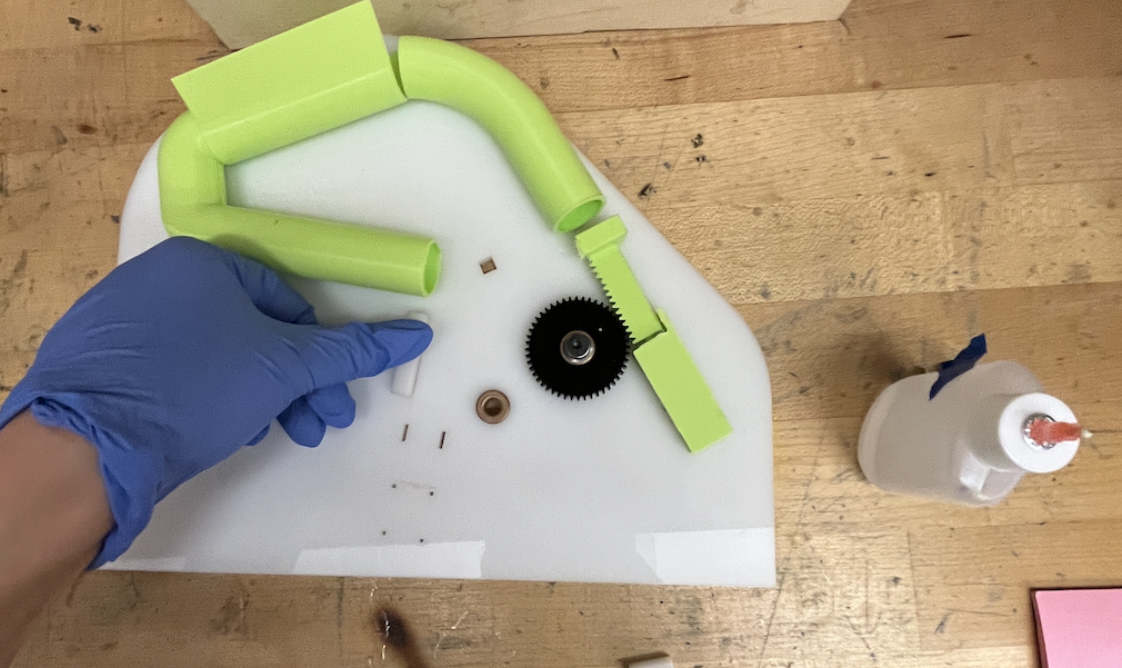

Reflections
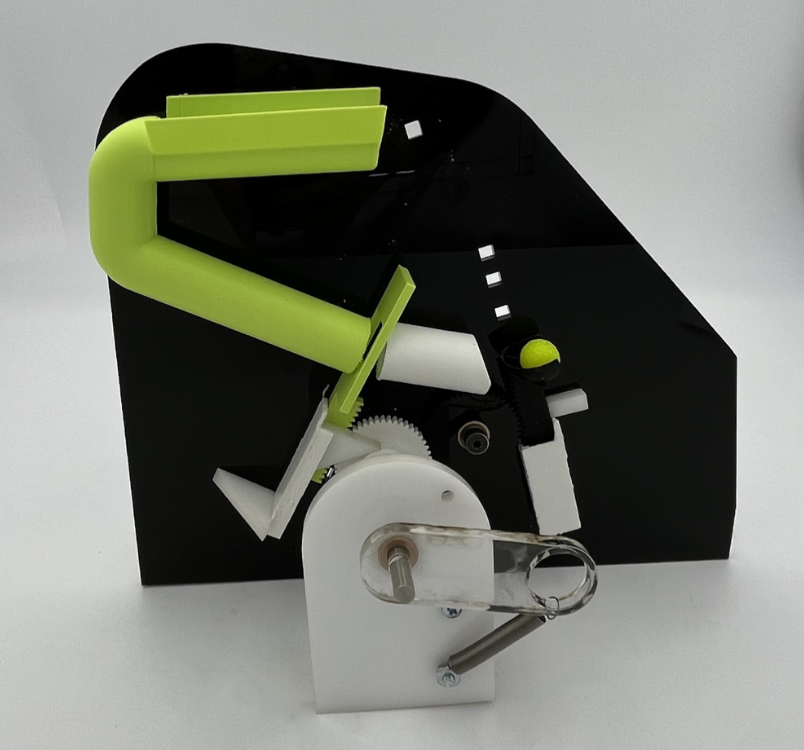
This course was my first exposure to Stanfords Product Realization Lab and to many new mechanical technologies:
I learned about accounting for physical factors like kerf and friction through iterative prototyping, and the value of pivoting in response to data. This was my first time working on an entirely mechanical project, and taught me valuable lessons in flexibility, ideation techniques, and technical skills.
- Heat Pressing
- Laser Cutting
- 3D Printing
- Autodesk Fusion 360
- Adobe Illustrator
I learned about accounting for physical factors like kerf and friction through iterative prototyping, and the value of pivoting in response to data. This was my first time working on an entirely mechanical project, and taught me valuable lessons in flexibility, ideation techniques, and technical skills.